Cracks in your concrete? Slabs starting to sink? You don’t need a sledgehammer solution — just the right one. Chemical grout injection offers a smart, noninvasive way to fix foundational issues. It fills hidden voids, seals cracks, and strengthens weak soil without...
What is Helicon’s Vibro Compaction Method of Densifying Soils?
Vibro compaction can be an excellent solution to densify soils in preparation for significant load bearing or to mitigate soil liquefaction. Vibro compaction methods use an industrial vibrator, or a vibroflot, to compact weak soils, increase bearing capacity and soil density. This is not to be confused with vibro replacement (stone column replacement) where crushed stone is filled into to hole created by the vibroflot.
Benefits
There are a few benefits to using vibro compaction and they include:
- fast and relatively economical pricing
- compaction work can be checked quickly and easily
- low noise and vibration levels
- environmentally friendly and uses local in situ material
- suited for soils with higher water tables
Soil Types
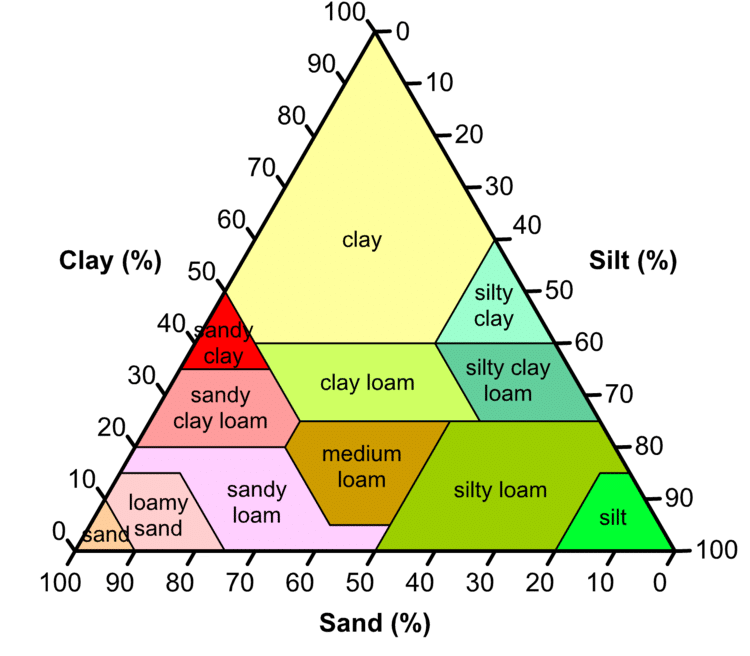
The soils that are in the area of operation significantly impact the effectiveness of vibro compaction. For example, vibro compaction works best with sandy soils (less than 12% silt fines) as there is more more space between each soil particle causing them to react more to compaction.
With silty sands, compaction is less effective, however still a good option. Soils that are comprised primarily of silts are the least affected by compaction as the soils are already compressed. Vibro compaction method reaches its technical limits where the fines content is high as with clay or any soils where fines are in excess of 15 to 20. This is because the fine particles cannot respond to the vibration and necessitate the need for vibro replacement instead.
Applications
Vibro compaction can be used for a number of different applications including:
- Buildings
- Airport taxiways
- Chemical Plants
- Storage Tanks
- Dams
- Pipelines
- Roads
- Residences
- Schools
- Hospitals
It is also important to note that vibro compaction methods are available for both on land and offshore applications like bridges, bridge approaches, highways, and highway overpasses.
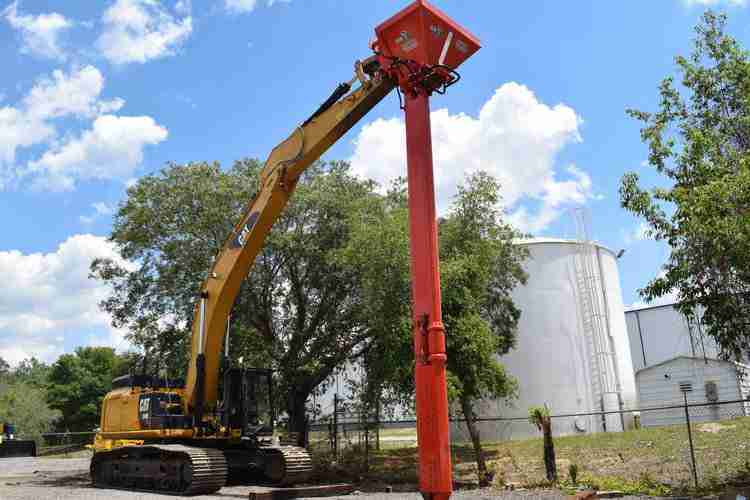
Penetration: penetrates to design depth and is surged up and down as necessary to agitate sand, remove fines, and form an annular gap around the vibrator. This stage of the process can either be used in conjunction with water pressure (wet top feed) or without water (dry bottom feed). Once the vibroflot has reached its design depth, the water is stopped or reduced if the water is present.
Process
COMPACTION
Under the action of induced horizontal forces, the soil particles surrounding the base of the vibrator are rearranged to a denser state of compaction. The vibrator is raised incrementally as compaction is achieved.
REFILLING
During compaction either imported or in situ material is introduced. If in situ material is used, the surface area being compacted may be lowered 5% to 15% of the treated depth.
COMPLETION
With an economical layout of compaction probes, an optimum improvement can be achieved. The surface of the improved area is then leveled and densified with a surface compactor.
For more information on either vibration method, both compaction, and replacement, you can read our Vibro compaction booklet HERE.