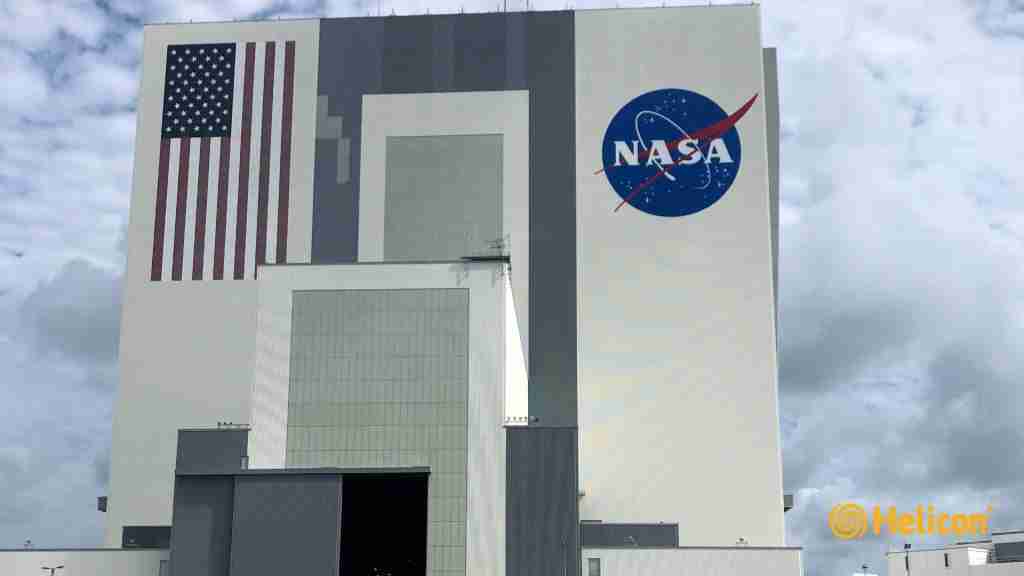
Cape Canaveral, FL
Client: NASA Kennedy Space Center
Market: Industrial
Solution: Ground Improvement
Services: Permeation Grout
The Project
The permeation grout project is at the NASA Kennedy Space Center in Cape Canaveral, FL. This project consisted of ground improvement for a heavily loaded slap stand structure that will be constructed along the transfer aisle between Highbays 3 & 4 in the Vehicle Assembly Building (VAB) which is located within the Launch Complex 39 area near the central portions of the Kennedy Space Center, Florida. This slap stand structure will be used in the servicing of the proposed Space Launch System vehicle (SLS).
Currently, the proposed slap stand is tentatively designed to bear directly upon the ground level floor slab of the VAB; hence, the degree of subsoil support beneath the floor slab section is of a critical concern. The Geotechnical Engineer of Record recommended a ground improvement solution of permeation grout pumped to improve the load bearing capacity of the existing soils at the site.
The Challenge
- Near-surface subsoils are fill soils that have a generally loose consistency transitioning to a medium dense at a depth of 5 feet.
- Loose fill materials are very susceptible to further densification and volume loss due to vibrations in the environment, and the effect of any downward water infiltration.
The Solution
Helicon worked alongside the geotechnical design team to develop a permeation grout program designed to meet the building code load criteria. Permeation grout injection pipes were driven on a center to center spacing of roughly 4 feet across each of the slap stand areas. The injection points were installed to a depth of at least 5 feet below floor slab grade. Grout was injected at a relatively low pressure (i.e. less than 50 psi) and grout needles were slowly withdrawn during pumping to render a uniform distribution of grout to about 3 feet below bottom of slab level. The amount of grout used was less than 15 gallons per foot per injection point.
As a final step, the existing voids beneath the floor slab were filled by the use of a two component polyurethane grout that produces a rigid structural foam. Injections of the poly foam system commenced at a depth of about 2 feet below slab level. Efficient planning & coordination was key to overcoming the challenges & limitations. Helicon collaborated with the Geotechnical Engineer of Record throughout the work and confirmed all recommended criteria were followed.
FREE INSPECTION REQUEST